04 Dec What Materials Are Used For Waterproofing?
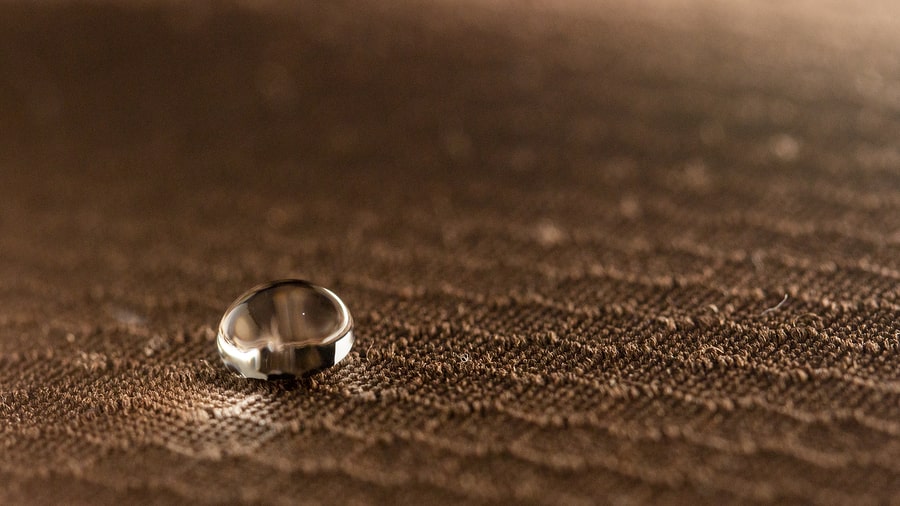
Waterproofing prevents your homes and offices from deteriorating. This includes protection from wear and tear, mould and water damages. It would be devastating for property owners to discover that water damages have damaged their properties.
A waterproofing contractor is needed to help property owners to adopt waterproofing preventive measures. This effectively protects the value and functionality of buildings. When done right, waterproofing goes unnoticed by the naked eye as it quietly protects your building.
The real question is what is waterproofing exactly?
Today we explore waterproofing at its core – how it is created, formed and chemically utilised.
A waterproofing membrane is a material that can be applied thinly over an area of surface. It can repel and prevent water from entering surfaces. A basic application of a waterproofing membrane is to spread it across the foundation of a building. This is done to reinforce the supporting structural blocks of the building by preventing water from damaging the property. A waterproofing membrane works best when it is applied to a sloped surface. Slanted angles allow for natural water runoff, thus preventing stagnation or ponding that would wear down the membrane.
A specialist waterproofing contractor should be an expert at identifying puddles. Although puddles are a natural occurrence for children to jump on and have fun in, waterproofing contractors detest and will prevent them from forming wherever possible. This is because when puddles exist for too long in an area, it will eventually seep into the surface and cause water damages.
What are the two types of waterproofing membranes?
The two commonly used waterproofing membranes are sheets and liquid-based membranes. They are usually within 2 to 4mm in thickness during the application process.
Sheet Based Membranes
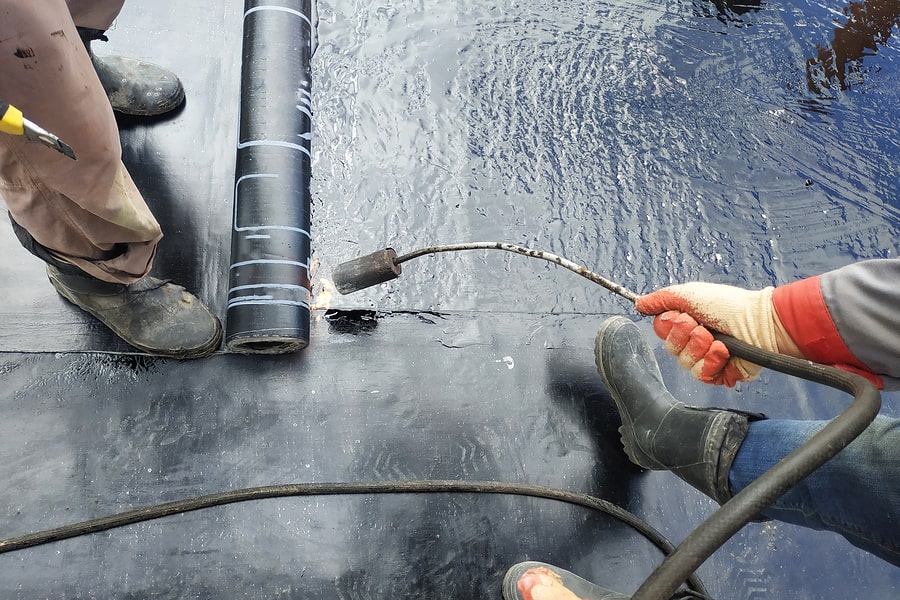
Sheet based waterproofing membranes, like its name suggests, are layers of sheets applied to a surface. This process is similar to putting up wallpapers but with waterproofing functionality. Bituminous waterproofing is a typical sheet-based membrane that is attached to the main surface by using a blowtorch together with a tar substance. This cohesion acts as an adhesive between the surface and the sheet membrane.
This method involves overlaying 100mm sheets to create a waterproof joint. This ensures that there are no gaps or potential leakage entry points to be found. On certain occasions, instead of blowtorches, a hot air gun is used to melt and fuse sheets. This waterproofs the initial layer of sheets. Specialised supervision and checks are very important as a single mistake can void the efforts of the entire surface area.
Besides, bituminous waterproofing membrane, there are other considerations you can take when sourcing for sheet-based membranes. The other options include PVC and composite membranes which consist of a fabric texture as a base. An additional chemical is applied to provide the membrane application with strength, durability and various types of resistance. The consistency of these membranes is equal due to being factory produced, strict testing and quality assurance.
Liquid Based Membranes
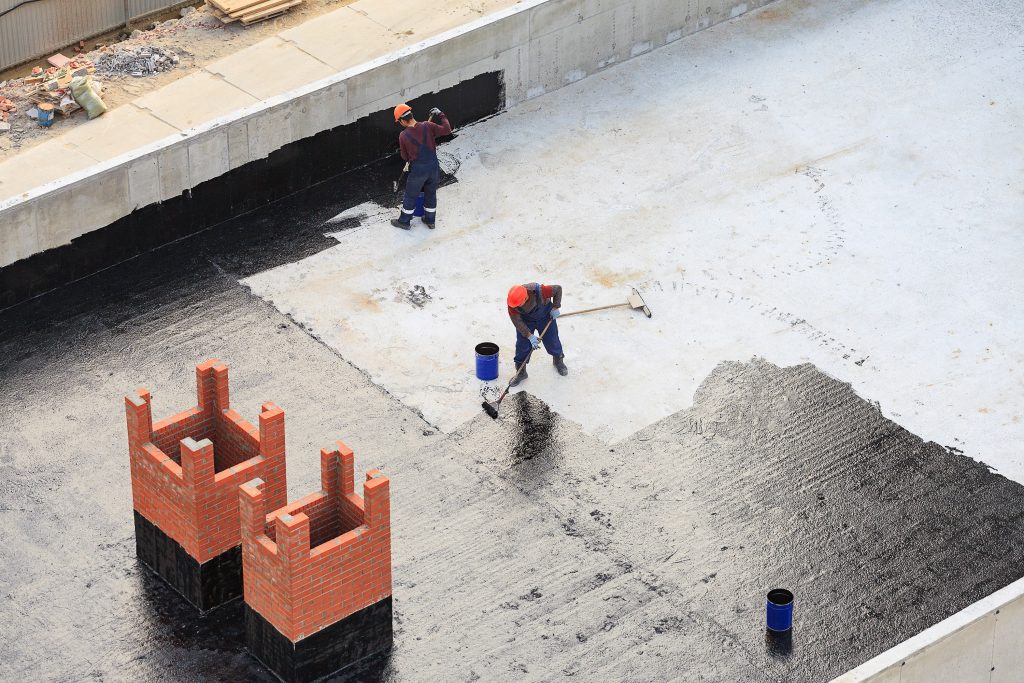
Liquid-based is a form of waterproofing membrane that comes in a liquid solution before the application on the target surfaces. Liquid application is usually sprayed or spread with roller brushes. When the liquid is sprayed, it settles on the surface quickly as it comes into contact with the air. When applied correctly, surfaces are completely covered and have consistent application. The way liquid application differs from sheet-based membrane is that they are much more flexible and can cover difficult areas such as curves, small gaps, and uneven spaces.
Crucially, proper implementation requires that the layer be completely laid in a single application. A waterproofing specialist is needed in this aspect as the job is time critical. Completing the application quickly prevents cold joints from occurring, thus preventing curing between the surface the liquid membrane. The risk of having inconsistent curing of both entities is the resultant gap created, which allows water to penetrate the surface.
Overall, liquid waterproofing application is deemed to be a greater option as compared to sheet-based applications because they are not restricted by joints. However, it is important to note that the thickness of the liquid-based membranes must be optimal for the entire waterproofing process to be successful. If there is a lack of sufficient membrane application, it might crack or fall off the surface. Before the application, it is also good to test the adhesiveness between the chemical and the surface.
In final considerations, if the liquid waterproofing membrane is applied before the application of the concrete layer, then a rougher surface needs to be created. This process is called sand broadcasting. Sand broadcasting involves the manual scattering of sufficient sand over a moist membrane that has yet to fully cure. As the sand slowly adheres to the membrane, it creates a rougher texture on the surface. This allows the concrete layer that is applied after, to properly stick to the surface.
Choosing the Right Waterproofing Membrane
Whether you choose a sheet or liquid-based waterproofing membrane, certain aspects should be consistent in any waterproofing membrane.
- UV Resistance: Most surfaces are in direct exposure with the sun, hence, this is an important aspect that a waterproofing membrane must have to prevent the material from degrading.
- Flexibility: Aside from cost and efficiency, the membrane must be able to stretch across distances. When the membrane is applied over surfaces like steel which will shift over time, it has to be able to stretch over cracks that might form.
- Air Ventilation: A quality membrane should be breathable to allow unforeseen trapped water to escape into the environment.
- Tear/Abrasion Resistance: Water proofing membranes should be tear and abrasion resistant due to the amount of physical friction that they are likely to encounter on a daily basis.
- Organic Interference: Resistance to common external factors like dirt and rain should be taken into consideration. Membranes are under constant exposure to such substances, and thus need to be durable in this aspect.
- Human Consumption Safety: Waterproofing membrane can come into contact with human consumption. An example would be waterproofing membranes on the insides of a water tank from which people attain water. Hence, consumer safety is an aspect that should not be neglected.
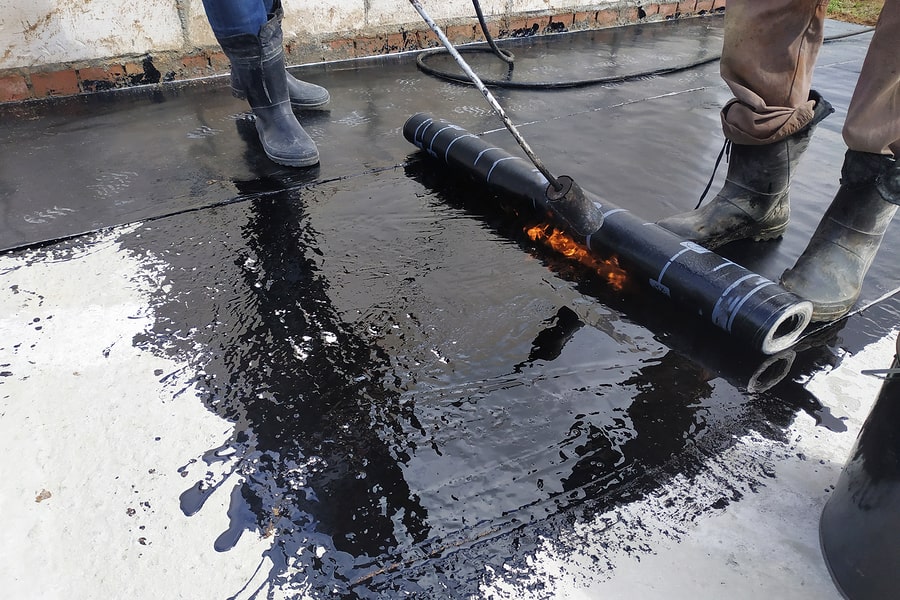
Trust TAC Contracts for Your Waterproofing Needs
TAC Contracts is an established and trusted waterproofing and repainting contractor. Over many years we continuously provided our customers with high-quality workmanship at very reasonable prices.
Our experienced contractors and specialists can help you in identifying, analysing and resolving your waterproofing issues. We use high quality waterproofing materials and recommend the appropriate waterproofing membranes for your building.
Sorry, the comment form is closed at this time.